UAE manufacturers accelerate Industry 4.0 adoption
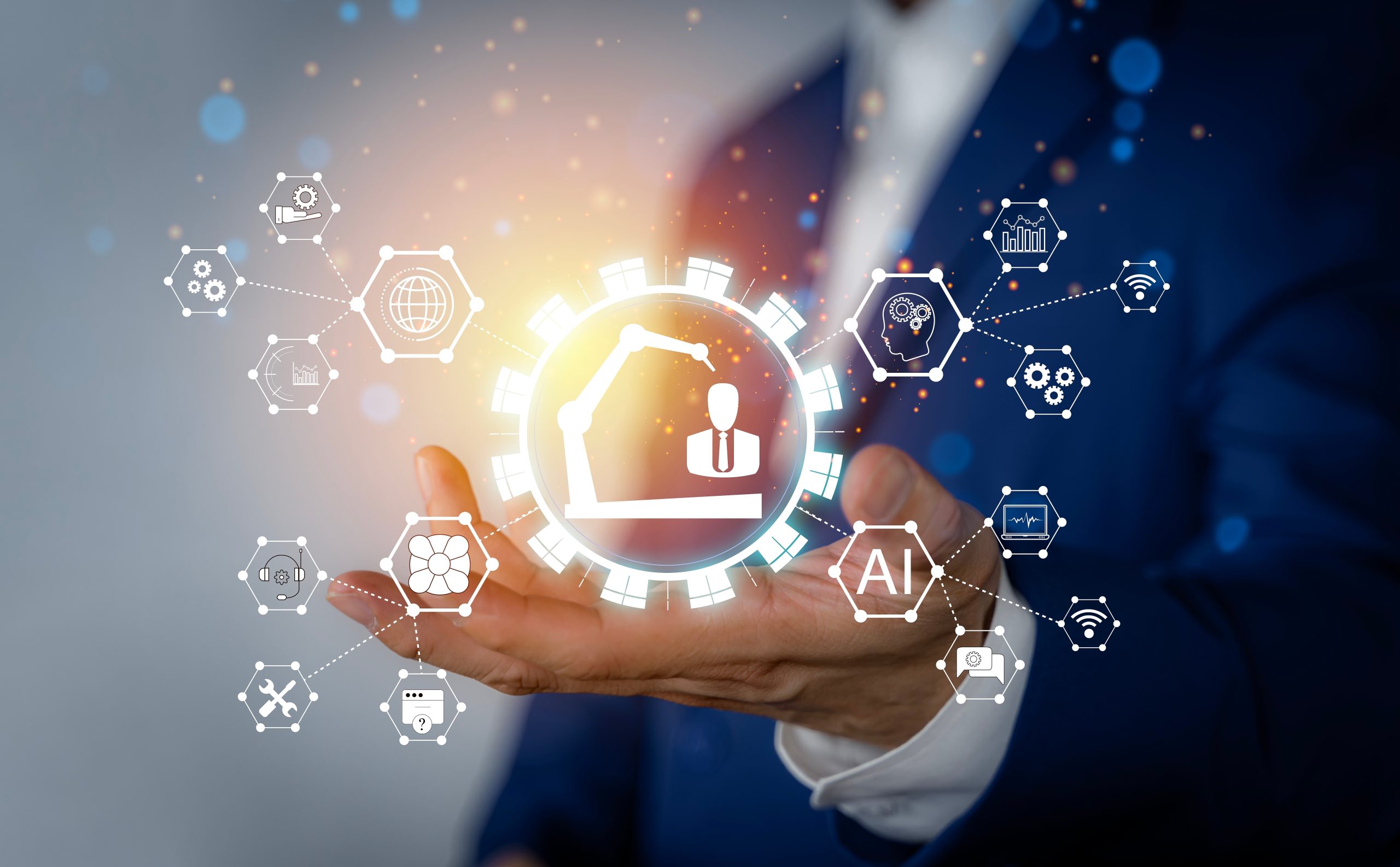
How the industry is deploying digital technologies to maximise efficiencies and improve client delivery
In 2021, as part of its efforts to remain at the forefront of technological innovation, the UAE’s Ministry of Industry & Advanced Technology (MoIAT) launched its Fourth Industrial Revolution Programme, also known as UAE Industry 4.0.
A key pillar of this push is Operation 300bn, a strategy aiming to grow national industrial GDP by 30% to AED300bn ($81.7bn) over the next decade. The policy will enhance overall industrial competitiveness, reduce costs, increase quality and efficiency, enhance safety and create new jobs in the region by providing a range of financial and non-financial incentives to accelerate technology adoption.
Backed by similar initiatives, manufacturing is on the path to becoming one of the most diverse industries in the region. Organisations are rapidly adopting innovative digital technologies to revolutionise operations and stay competitive in an ever-evolving market.
“Manufacturing is transforming into a technologically advanced industry in the region, with 30- to 40-year-old processes being re-engineered to provide more agile and productive manufacturing outcomes,” said Mohammed Ameen, chief information officer at Masafi Group, at the recent Mashreq MEED Manufacturing Summit.
As dynamic changes continue to influence the manufacturing landscape, industry leaders must make strategic decisions regarding the allocation of investments in new technologies, identifying those that will yield the maximum benefit to their organisations.
Driven by adoption
The World Economic Forum regards the manufacturing industry as one of the key drivers of the global economy, accounting for about 22% of employment worldwide.
Digital technologies such as automation, artificial intelligence (AI) and the industrial internet of things (IIoT) have played a considerable role in optimising industrial processes, minimising waste and improving quality control. However, the most significant impact brought by the industry is the emergence of Industry 4.0, or 4IR, and its potential to create smart factories that are highly automated, data-driven and fully connected to supply chains.
According to McKinsey, by harnessing these types of tools, companies have reported a 30%- 50% reduction in machine downtime, a 15%-30% increase in labour productivity and a 10%-20% decrease in quality costs.
Integrating these smart technologies into manufacturing processes has enabled real-time communication, remote monitoring and data collection toolsets, leading to unprecedented advances in quality, reliability and agility.
Additionally, smart factory transformations generate productive, operator-friendly, energy-efficient solutions that have progressively taken over traditional workflows.
In the era of Industry 4.0, a proactive maintenance approach relies on the integration of interconnected devices. Sensors play a crucial role in conveying data to IIoT networks and facilitating the prioritisation of interventions by maintenance and operations teams.
A case in point is the global process implementation company Krohne, which is actively engaged in the field of instrumentation and delivering industrial sensor technology for data collection.
“The presence of multiple data points makes it difficult to streamline automation processes,” said Jay Gadhavi, general manager of the Middle East and Africa at Krohne. “The integration of IoT helps in the seamless collection and real-time distribution of valuable data across robust networks.”
At Krohne, digital twin technologies have positively impacted its ability to forecast demand accurately. For instance, the PipePatrol internal leak detection system provides real-time analytics and alerts to reduce oil wastage, leading to lower environmental impacts.
The push towards digital adoption is encouraging several businesses to reassess their operations and design solutions to keep up with the changing times.
“One of the key pillars of our Industry 4.0 journey is smart manufacturing,” said Shakti Arora, chief procurement officer at RAK Ceramics, a premium ceramics lifestyle solutions manufacturer.
“We are working towards bringing infrastructure-level changes by revolutionising our supply chains, understanding machine outputs, focusing on predictive maintenance and optimising energy savings.”
Adopting a collaborative manufacturing model has helped RAK Ceramics reduce its electricity consumption by 35% over the past five years. The company also emphasises circular practices and has committed to 100% waste recycling.
Externally, the manufacturer launched its first smart tiles factory in Ras Al Khaimah. The factory features smart tiles automation and IoT technologies to optimise production, reduce waste and enhance product quality.
Fast-moving consumer goods companies also use AI for product innovation and consumer insights. To align with digitisation trends, Masafi Group has similarly launched a smart factory in Fujairah.
“We aim to digitise data by extracting information from various machines, which will, in turn, help us analyse line efficiencies, identify points of breakage and implement predictive maintenance strategies,” said Ameen.
“By delving into inventory management, we can assess manual labour requirements, power efficiency and water capacities.”
He adds that such implementations are necessary for the agility and efficiency required to maintain a competitive edge.
Government-led initiatives
The UAE continues to implement programmes across various disciplines, encouraging the adoption of Industry 4.0.
These programmes are equipped to provide access to expertise and technology, drive research and development projects, generate intellectual property for the industrial sector, and offer access to funding for digital transformation and Industry 4.0 manufacturing facilities.
Gadhavi agrees that the six pillars of this Industry 4.0 strategy provide an ideal framework to guide companies and stakeholders to make better decisions.
The framework focuses on evaluating the readiness of governments for the next decade against six main criteria: technology and innovation, economy, society, natural resources and the environment, security and governance.
To bolster its position as a key industrial hub in the Middle East, Abu Dhabi’s Department of Economic Development has introduced a smart manufacturing index to help local companies use Industry 4.0 technologies to boost productivity and contribute to the economy.
The index aims to equip manufacturers with essential expertise and education on Industry 4.0 technologies.
Additionally, it will outline a comprehensive roadmap for manufacturers involving the assessment of a production facility’s present status, strategies to enhance preparedness levels, suggested actions to upgrade facilities and identification of optimal production approaches to leverage the transition to advanced manufacturing.
While the launch of these initiatives has stirred positive conversations and yielded successful outcomes, more must be done to address the need and generate a unified action among companies.
“It is important for companies to engage in meaningful internal conversations,” said Gadhavi. “Businesses should assess the potential impacts of embracing such technologies and evaluate how they can leverage them to elevate their operations to the next level.”